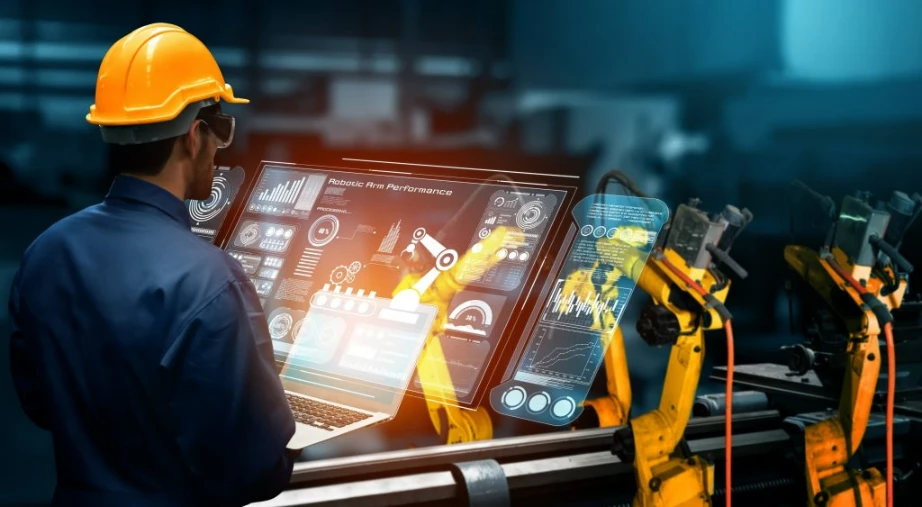
One industry that is reaping the benefits of emerging advancements in AI is manufacturing. With manufacturing systems becoming increasingly dynamic and complex, fully automated production lines and smart manufacturing are becoming the need of the hour. Addressing this need, AI is driving substantial innovation by reshaping traditional production systems into “smart factories” which today are also known as “Industry 4.0. or 4IR”. So what is Industry 4.0? It is the exchange of data and technologies like machine learning, cloud computing, robotics, machine vision, and similar technologies that provide real-time analysis of various manufacturing processes. Here are a few examples of how AI’s intelligent & connected technologies are enabling smart production:
Collaborative manufacturing
As of 2020, the International Federation of Robotics (IFR) estimates that 1.64 million industrial robots will oversee manufacturing processes worldwide. Robots will utilize machine learning algorithms or self-learning algorithms to handle production processes better, reduce the susceptibility to human error and also improve productivity in labor intensive settings.
With this human-robot collaboration (HRC), manufacturing processes will overcome several challenges including those of greater cognitive complexity and benefit from real-time data-based decision-making. Taking over roles that are undesirable, repetitive, or dangerous a collaborative robot will save costs related to a human’s physical limitations and optimize workflows to streamline production processes.
Predictive maintenance
A well-known application of industrial AI, predictive maintenance uses algorithms to perform a maintenance check on a component, machine, or system to predict when it would undergo failure. Using digital twins, sensors, and advanced analytics to precisely assess a machine’s condition on an up-to-the-minute basis, predictive maintenance gives real time updates that surpass the need for performing preventive maintenance.
An example of its niche application is using IoT & machine learning in the production of titanium implants. Special tools with diamond tips are required to cut through titanium’s hardness. When predictive maintenance in combination with machine learning techniques is implemented, the vibrations, sound sensors, and torque monitors help evaluate dulling of tooltips thus suggesting the optimal time to sharpen them.
The application of predictive maintenance for its potential benefits includes detection and elimination of equipment defects and condition-based monitoring and includes the prevention of unplanned downtime of machines.
Digital twins
Internet of Things (IoT) with its network of sensors & cameras enable several manufacturing operations. When the data derived from sensors that monitor millions of devices is combined with machine learning, real-time information of a machine can trigger the production of newer models and prototypes of older versions or even 3D printed spare parts to replace redundant ones.
Among its many applications, digital twins would enable the creation of a virtual copy of a product, service, process, equipment, or even a supply chain and improve it using data. With sensors grasping the accurate configuration of the actual product or equipment they scan, a digital twin will optimize its performance by monitoring the physical item’s position and status with live updates.
When these updates are shared with a cloud, it will give vital insights into the manufacturing process. The digital twin technology is currently being applied to the designing of products, recalibration of equipment, reduction of variances in production, and monitoring product quality.
Computer vision
A computer vision system is a set of high-resolution cameras, optics integrated with AI to provide a quantitative assessment of a product. Where the human vision is unable to, computer or machine vision tools through their greater speed, accuracy, and ability are able to capture anomalies in the production process. Computer vision not only “sees” but also processes and eventually “learns” from what it sees. An example of this technology is the use of an advanced algorithm that alerts the manufacturer through a process called “automated issue-identification”, particularly in defect detection.
Through several such & many more applications in the product assembly process like 3D vision systems, barcode analysis, safety & security, and management of inventory, computer vision is enabling the emergence of innovative models in production and ‘smart’ products.
Shaping the future
It is estimated that smart factories will generate $37 trillion through the implementation of AI by 2025. (source – McKinsey & Company) As technology advances in AI, especially in machine learning (ML), it shows great potential in transforming the manufacturing sector. As one of the industries that generate more data than any other, manufacturing has more to gain not only through AI’s ability to process vast amounts of data but also through its useful tools & technological subsets. Making it highly responsive to customer’s changing needs and the ever-evolving market landscape, AI is bound to empower manufacturing in the coming years.